In the ever-evolving world of manufacturing, the ability to withstand harsh environments is a critical factor that can determine the success or failure of operations. This article delves into the significance of harsh environment suitability in the manufacturing industry, exploring why it is essential and how it impacts various aspects of production.
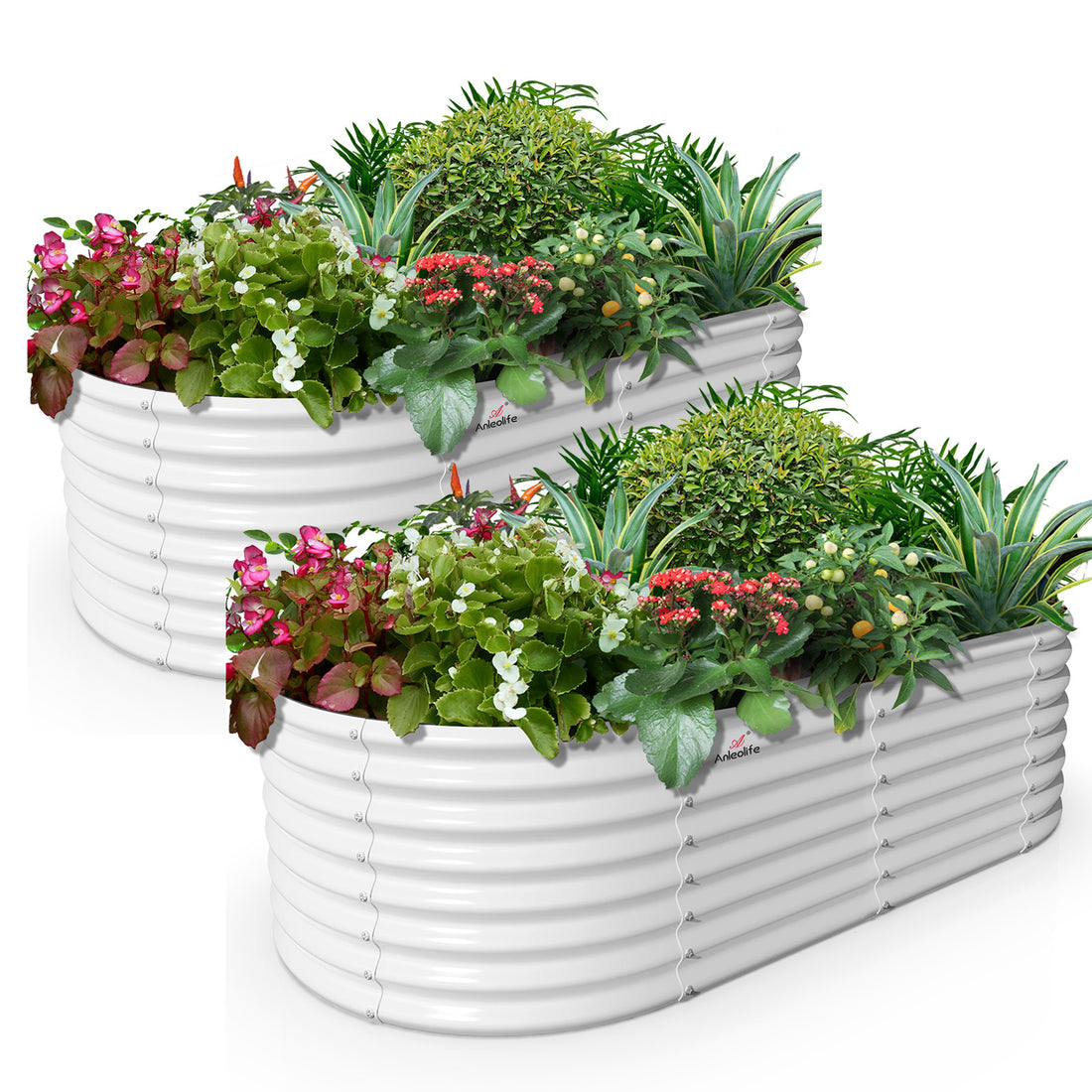
The Necessity of Harsh Environment Suitability
Manufacturing environments are often characterized by extreme conditions such as high temperatures, corrosive substances, heavy machinery, and continuous operation. Harsh environment suitability ensures that equipment and materials can endure these conditions without compromising performance or safety. For instance, in the chemical manufacturing sector, machinery must resist corrosive chemicals to prevent breakdowns and ensure worker safety.
Impact on Equipment Longevity and Maintenance
One of the primary benefits of ensuring harsh environment suitability is the extended lifespan of equipment. When machinery is designed to withstand extreme conditions, it experiences less wear and tear, leading to fewer breakdowns and lower maintenance costs. For example, in the mining industry, equipment exposed to abrasive materials and high-impact operations must be robust to avoid frequent replacements and repairs.
Enhancing Operational Efficiency
Harsh environment suitability directly contributes to operational efficiency. Equipment that can operate reliably under adverse conditions reduces downtime, ensuring continuous production. In the oil and gas industry, for instance, drilling equipment must function efficiently in extreme temperatures and high-pressure environments to maintain steady production rates.
Ensuring Worker Safety
Worker safety is paramount in any manufacturing setting. Equipment and materials that are suitable for harsh environments help mitigate risks associated with extreme conditions. For example, in the aerospace industry, materials used in aircraft manufacturing must withstand high temperatures and pressure variations to ensure the safety of both workers and end-users.
Cost Implications and Economic Benefits
Investing in equipment and materials that are suitable for harsh environments can lead to significant cost savings in the long run. While the initial investment may be higher, the reduction in maintenance costs, downtime, and replacements can result in substantial economic benefits. For instance, in the automotive industry, using corrosion-resistant materials in manufacturing can reduce the frequency of part replacements, leading to cost savings and improved profitability.
Innovative Materials and Technologies
The development of innovative materials and technologies plays a crucial role in enhancing harsh environment suitability. Advanced composites, coatings, and alloys are being engineered to withstand extreme conditions, offering manufacturers a range of options to improve their operations. For example, the use of advanced ceramics in high-temperature applications provides superior performance compared to traditional materials.
Conclusion
Understanding the importance of harsh environment suitability in the manufacturing industry is essential for ensuring the longevity, efficiency, and safety of operations. By investing in robust equipment and materials, manufacturers can achieve significant economic benefits, enhance operational efficiency, and ensure worker safety. As technology continues to advance, the development of innovative solutions will further improve the ability to withstand extreme conditions, driving the industry forward.